An Overview of the Phonograph Record Manufacturing Process
<<< Back to Custom Disk Recording and Mastering Systems
Stage 1: MASTERING
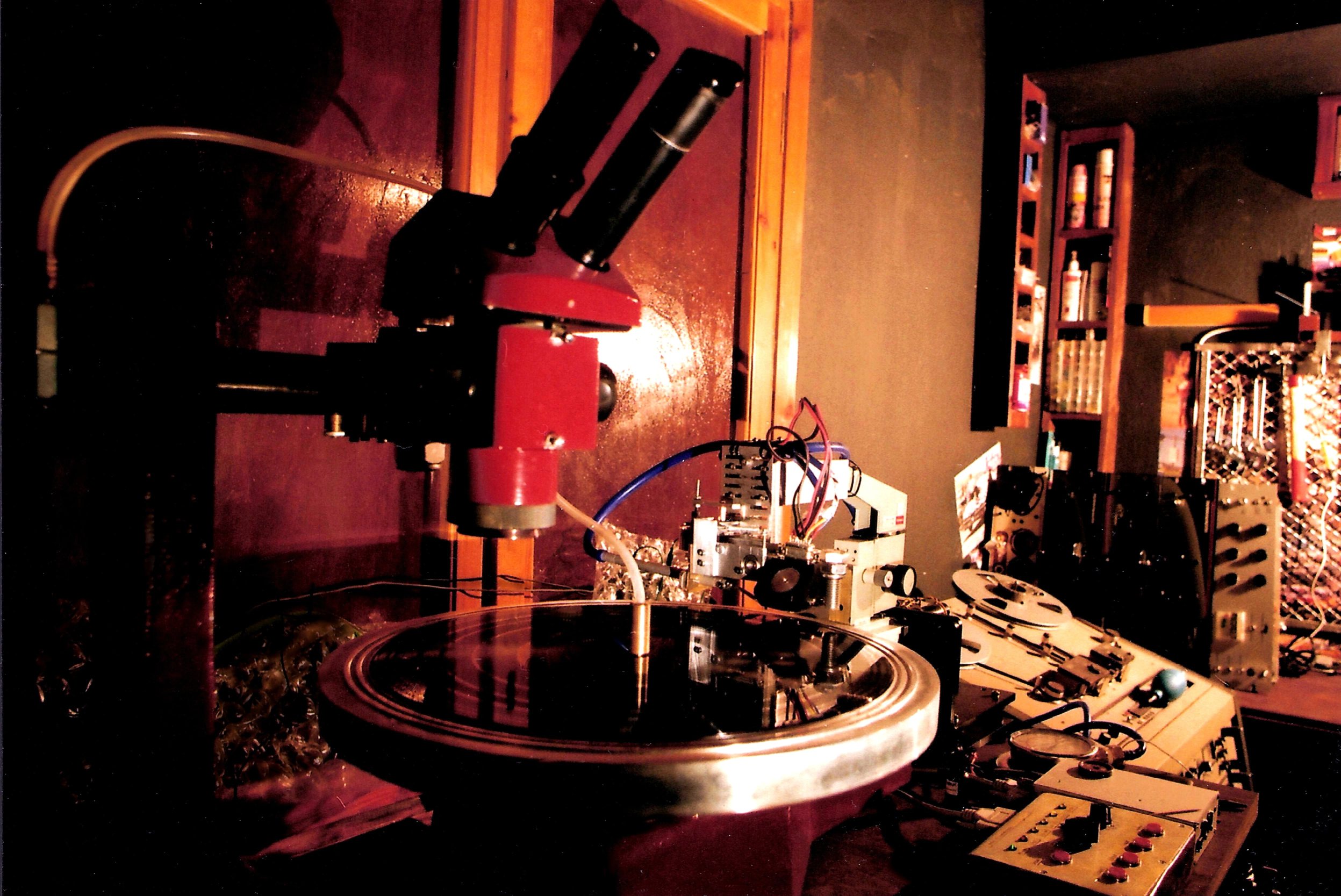
The audio is reproduced from the source medium on which it was stored during the recording/mixing/premastering process and reaches the disk mastering system in the form of an analog electrical signal, which drives the coils of the cutterhead into motion. This motion is transmitted to the cutting stylus, which cuts a spiral groove, modulated by the sound, on the surface of the master disk. The master disk, often also referred to as a "lacquer disk", is a metallic substrate with a coating of soft lacquer. When the grooves have been cut, the master disk contains the exact grooves that will be transferred to the final product, the vinyl record, by the end of the manufacturing process. The sound quality of the final product and the accurate transfer of the information contained within the source medium are primarily defined by the disk mastering process, the performance of the disk mastering equipment and the skill of the disk mastering engineer.
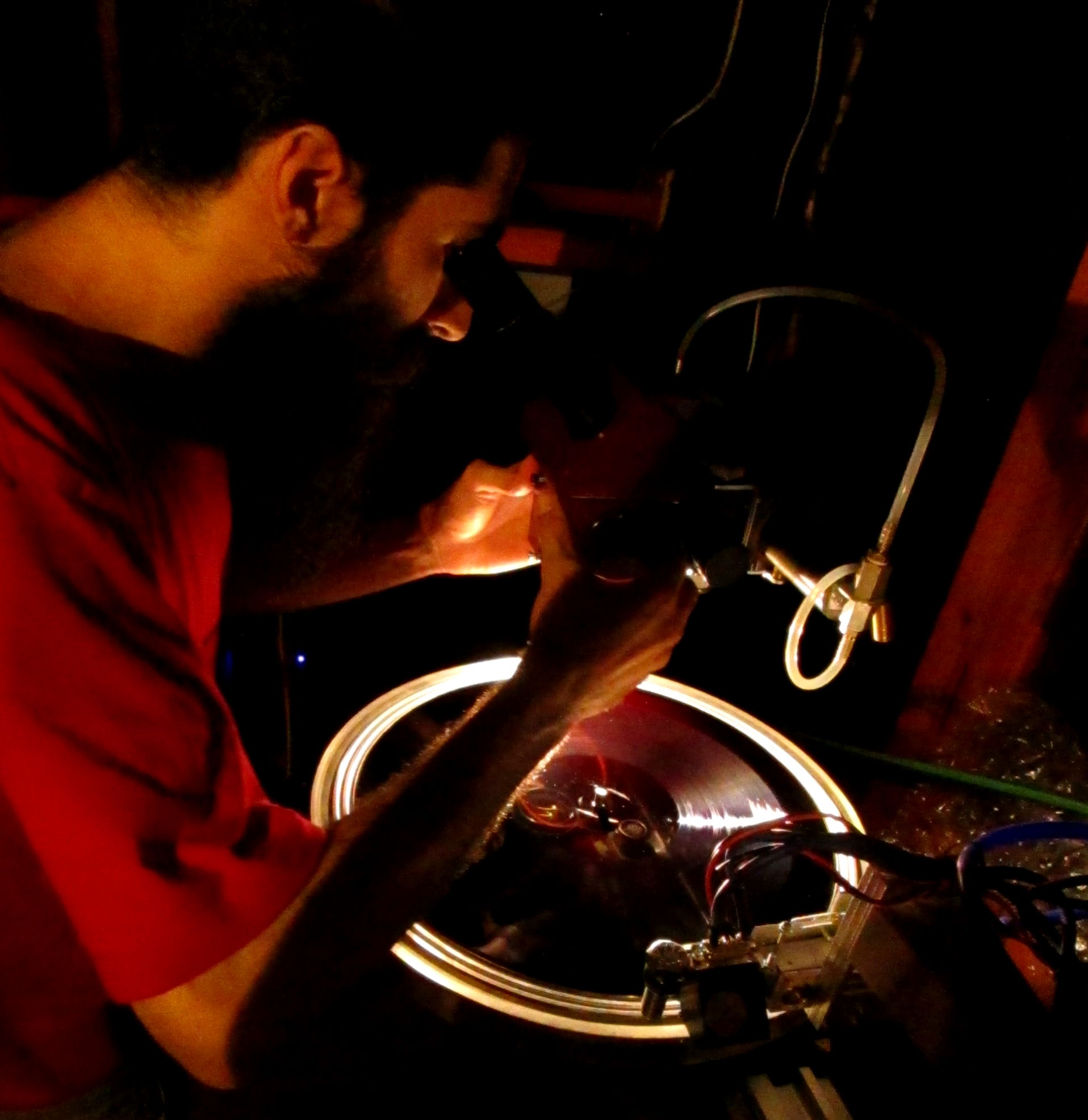
Stage 2: PLATING
The freshly cut master disks are sent to the plating facility, where they will undergo various stages of cleaning and chemical treatment, before being sprayed with a conductive silver coating. They are then subjected to an electrochemical plating process, during which a metallic "negative" of the master disk is produced. When the negative is separated from the master disk, it features "ridges" instead of grooves. The outcome of the plating stage are two metallic stampers, one for each side of the record, which will be used in the following stage to manufacture the multiple copies of the vinyl records.
Stage 3: PRESSING
The stampers are sent to the pressing facility, where they are mounted in the molds of a hydraulic press, with a puck of extruded vinyl placed in between them, along with the paper labels. Under high temperature and pressure, the stampers flatten out the puck and stamp the grooves into it, forming it into the familiar shape of the vinyl record. The first few pressed records are considered test pressings and are shipped out to the mastering engineer, the recording engineer, the producer, the musicians and other interested parties for quality control and approval. The test pressings offer the first opportunity to reproduce and evaluate the transfer of the sonic information onto the grooves, since the master disk cannot be reproduced without damage. If the test pressings are approved, the pressing cycle is repeated until the desired number of vinyl records have been manufactured. If any problems are identified during the evaluation of the test pressings, they have to be traced back to their origin and rectified, prior to proceeding with the manufacturing. A new set of test pressings will be used to ensure that it sounds like it should, following any changes made in any of the three stages of manufacturing.